Understanding Die Casting Injection Molding: A Comprehensive Guide
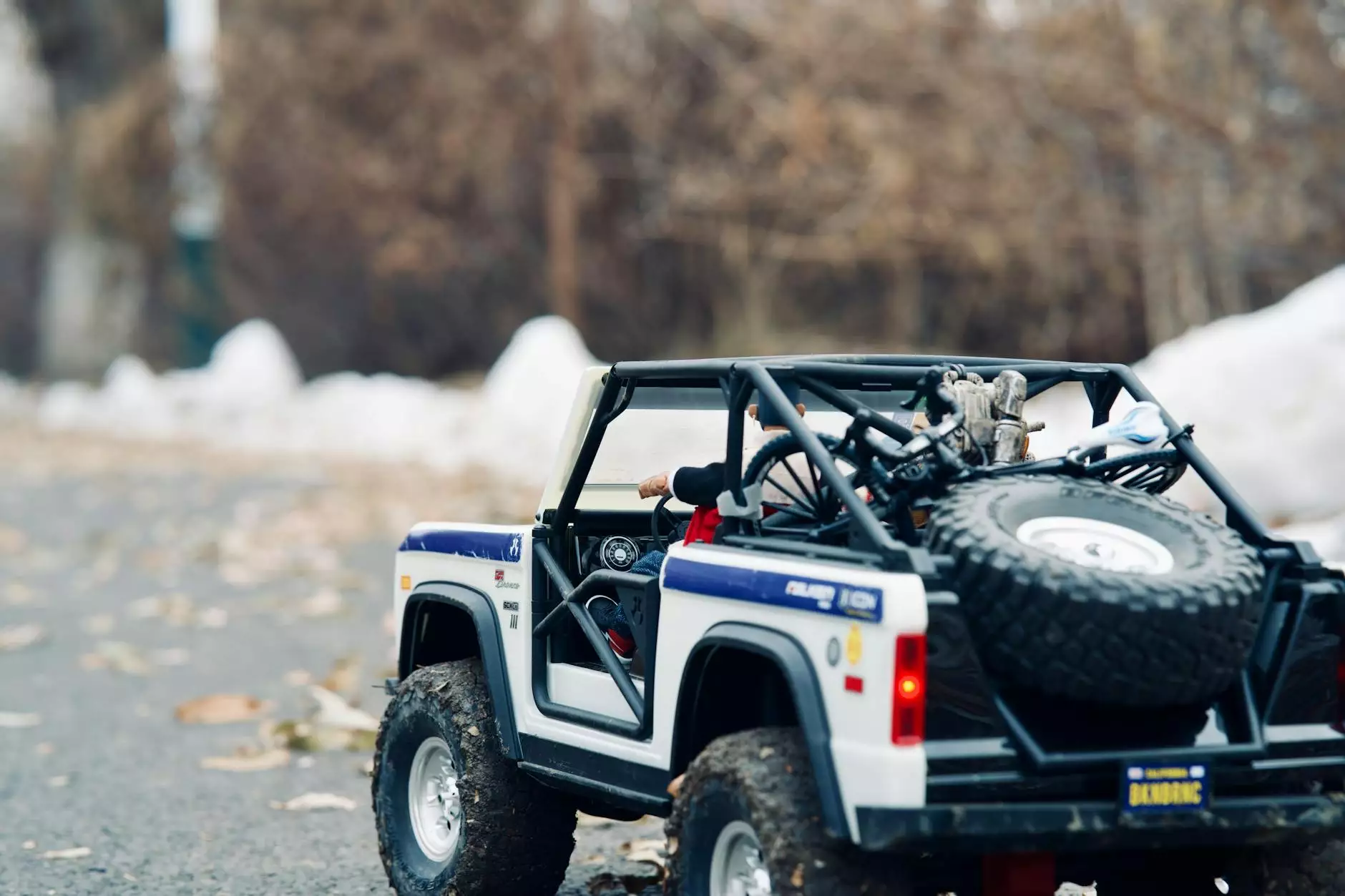
What is Die Casting Injection Molding?
Die casting injection molding is a manufacturing process that involves forcing molten metal into a mold cavity under high pressure. This method is primarily used for producing intricate and precise metal parts with a smooth surface finish and tight tolerances. Understanding this process is crucial for industries that depend on high-quality metal components, including automotive, aerospace, and electronics.
The Key Components of Die Casting Injection Molding
There are several essential components in the die casting injection molding process:
- Mold: Typically made from steel or other durable materials, the mold is designed to give the final product its shape.
- Injection System: This component is responsible for injecting the molten metal into the mold cavity.
- Metal Alloy: Common alloys used include aluminum, zinc, and magnesium. Each offers unique properties suitable for different applications.
- Ejector System: Once the metal has cooled and solidified, this system ejects the finished part from the mold.
A Step-by-Step Breakdown of the Die Casting Process
The die casting injection molding process can be broken down into several key steps:
- Mold Preparation: The mold is prepared and clamped securely to prevent any leakage of molten metal.
- Melting the Alloy: The chosen metal alloy is heated to its melting point in a furnace.
- Injection: The molten metal is injected into the mold under high pressure, filling all cavities.
- Cooling: The metal cools and solidifies within the mold, taking its final shape.
- Ejection: Once cooled, the ejector pins push the newly formed part out of the mold.
- Trimming and Finishing: Any excess material is trimmed, and final finishing processes are carried out to ensure quality.
Types of Die Casting
There are two main types of die casting injection molding processes:
- Hot Chamber Die Casting: This method is suitable for metals with low melting points. The injection mechanism is immersed in the molten metal, allowing for quicker cycles.
- Cold Chamber Die Casting: This process is ideal for metals with higher melting points and involves a separate chamber for melting the alloy before it is injected into the mold.
Applications of Die Casting Injection Molding
The die casting injection molding process is utilized across various industries due to its versatility and efficiency:
- Aerospace: Precision parts for aircraft, including housings, brackets, and components.
- Automotive: Manufacturing lightweight parts for vehicles, such as engine blocks, transmission cases, and wheels.
- Electronics: Creating enclosures and parts for various electronic devices.
- Consumer Goods: Developing durable and stylish products ranging from appliances to tools.
The Benefits of Die Casting Injection Molding
Choosing die casting injection molding as a manufacturing method offers several significant advantages:
- Precision and Detail: The process allows for tight tolerances and intricate designs, reducing the need for extensive machining.
- Cost-Effectiveness: With high production rates, this method significantly lowers costs per unit for large runs.
- Material Efficiency: Minimal waste is generated, making it an environmentally friendly option.
- Durability: Components produced through die casting are typically stronger and more robust than those made by other methods.
- Surface Finish: Die casting provides an excellent surface finish, reducing the need for additional finishing processes.
Quality Control in Die Casting Injection Molding
Quality control is critical in the die casting injection molding process. Manufacturers employ several methods to ensure that each part meets stringent specifications.
Techniques such as:
- Dimensional Inspection: Verifying key dimensions against design specifications.
- Visual Inspection: Checking for surface defects like cracks or voids.
- X-ray Analysis: Examining the internal structure for possible inconsistencies.
are essential to maintaining high-quality production standards.
Choosing the Right Die Casting Partner
Selecting a die casting injection molding partner requires careful consideration. Key factors to evaluate include:
- Experience and Expertise: Look for a partner with extensive experience in the industry and a proven track record of successful projects.
- Technology and Equipment: Ensure they utilize modern, high-quality equipment for optimal results.
- Quality Assurance Processes: Verify their commitment to quality control and continuous improvement.
- Customer Support: Evaluate their responsiveness and willingness to collaborate throughout the project.
Future Trends in Die Casting Injection Molding
The future of die casting injection molding is poised for exciting advancements. Trends to watch include:
- Automation: Increased automation in the casting process will enhance efficiency and accuracy.
- Eco-Friendly Practices: A growing emphasis on sustainability will lead to the development of greener materials and processes.
- 3D Printing Integration: Combining traditional die casting with additive manufacturing techniques for innovative designs.
Conclusion
The die casting injection molding process is a cornerstone in the realm of metal fabrication, offering numerous advantages in terms of precision, efficiency, and durability. Understanding this method is essential for businesses looking to benefit from high-quality metal components. As industries evolve, embracing the latest trends and innovations will be key to staying competitive and meeting the demands of a fast-paced market.
For more insights into die casting and various metal fabrication methods, visit DeepMould.net, where we provide expert guidance and solutions tailored to your needs.