The Significance of Injection Molding Makers in Manufacturing
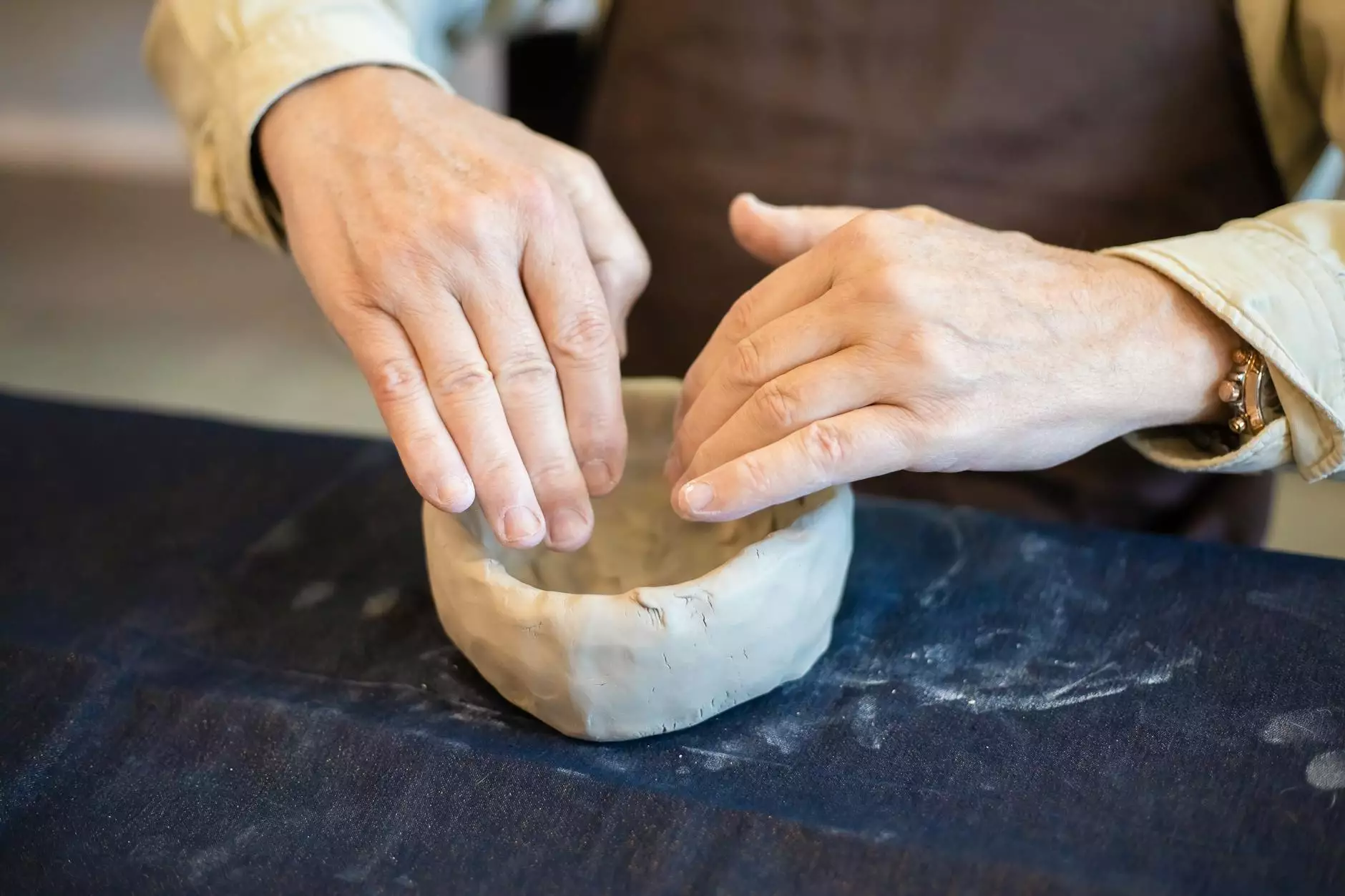
The world of manufacturing is vast and complex, encompassing a myriad of processes that contribute to the creation of products we use daily. Among these processes, injection molding stands out as a cornerstone technique in the production of precision parts and components. At the center of this essential manufacturing process are the injection molding makers, who play a pivotal role in driving innovation and efficiency within the industry.
Understanding Injection Molding
Injection molding is a highly efficient manufacturing process used primarily for producing parts by injecting materials into a molded cavity. This technique typically employs thermoplastic and thermosetting materials, which are heated and injected into a mold under high pressure. Once the material cools, it solidifies into the desired shape.
Why Choose Injection Molding Makers?
Choosing an experienced injection molding maker offers several advantages that can significantly impact your manufacturing operations:
- Precision and Accuracy: Injection molding allows for high tolerance levels, enabling the production of intricate designs with precision.
- Scalability: Once the initial tooling is produced, manufacturers can scale up production efficiently, making it ideal for both small and large-scale production runs.
- Material Versatility: Injection molding can accommodate a diverse range of materials, including plastics, metals, and composites.
- Cost-Effectiveness: For mass production, injection molding can be more cost-effective compared to other manufacturing processes, thanks to its speed and minimal waste.
The Role of Metal Fabricators in Injection Molding
While injection molding makers are primarily associated with plastic production, the role of metal fabricators cannot be overlooked, especially in hybrid applications where metal components are integrated or reinforced. Metal fabricators contribute to the injection molding industry in various ways:
- Tooling and Die Creation: These professionals create the molds needed for injection molding processes. A well-made die is crucial for ensuring the final products meet stringent specifications.
- Quality Control: Metal fabricators often implement rigorous quality control measures to ensure that molds are manufactured to exacting standards.
- Material Innovation: Collaborations between injection molding makers and metal fabricators are leading to innovative materials that enhance product durability and performance.
Innovations in Injection Molding Technology
Automation and Industry 4.0
The integration of automation in injection molding processes is revolutionizing productivity and efficiency. By employing robotic systems for part handling and assembly, injection molding makers can minimize human error and enhance safety in the manufacturing environment. The move towards Industry 4.0 has further propelled this revolution, allowing for real-time data tracking and advanced analytics in production systems.
3D Printing and Rapid Prototyping
The advent of 3D printing technology has transformed how injection molds are designed and produced. Rapid prototyping techniques allow injection molding makers to quickly create prototypes for testing, reducing time-to-market and iterating designs based on real-time feedback. This has led to significant advancements in product development cycles.
Choosing the Right Injection Molding Maker
When selecting an injection molding maker for your next project, consider the following factors to ensure you choose the best partner for your business:
- Experience and Expertise: Look for manufacturers with a proven track record in your specific application area.
- Technology and Equipment: Ensure the company invests in modern, state-of-the-art machinery that can accommodate your production needs.
- Quality Assurance Processes: Evaluate their quality control measures and certifications to guarantee product consistency.
- Customer Support: A reliable partner should provide excellent customer service and support throughout the production process.
- Customization Capabilities: The ability to customize molds and adapt to your specific requirements is crucial for achieving desired outcomes.
The Future of Injection Molding
As industries continue to evolve, the future of injection molding makers looks promising. Sustainable practices are becoming increasingly important; hence, the industry is leaning towards eco-friendly materials and manufacturing processes. Innovations in bio-based plastics and recycled materials are changing the landscape of production, making it more environmentally friendly.
Embracing Sustainability
Many injection molding makers are actively working towards reducing their carbon footprint by optimizing processes that minimize waste. This includes:
- Utilizing recycled materials in production.
- Implementing energy-efficient machinery.
- Reducing water usage during manufacturing processes.
- Innovating with biodegradable plastics that decompose faster than traditional materials.
Conclusion
In conclusion, injection molding makers are indispensable in today's manufacturing landscape, providing precision, scalability, and cost-effectiveness. Their collaboration with metal fabricators enhances the industry, pushing the boundaries of innovation. As manufacturing technologies continue to advance, choosing the right injection molding maker can significantly affect your product's success. By staying ahead of trends such as automation and sustainability, businesses can ensure they remain competitive in a rapidly changing market.
To explore how DeepMould can assist with your injection molding needs, visit our website and discover our comprehensive offerings in metal fabrication and injection molding technology.