The Essential Role of a Plastic Mold Manufacturer in Today's Business Landscape
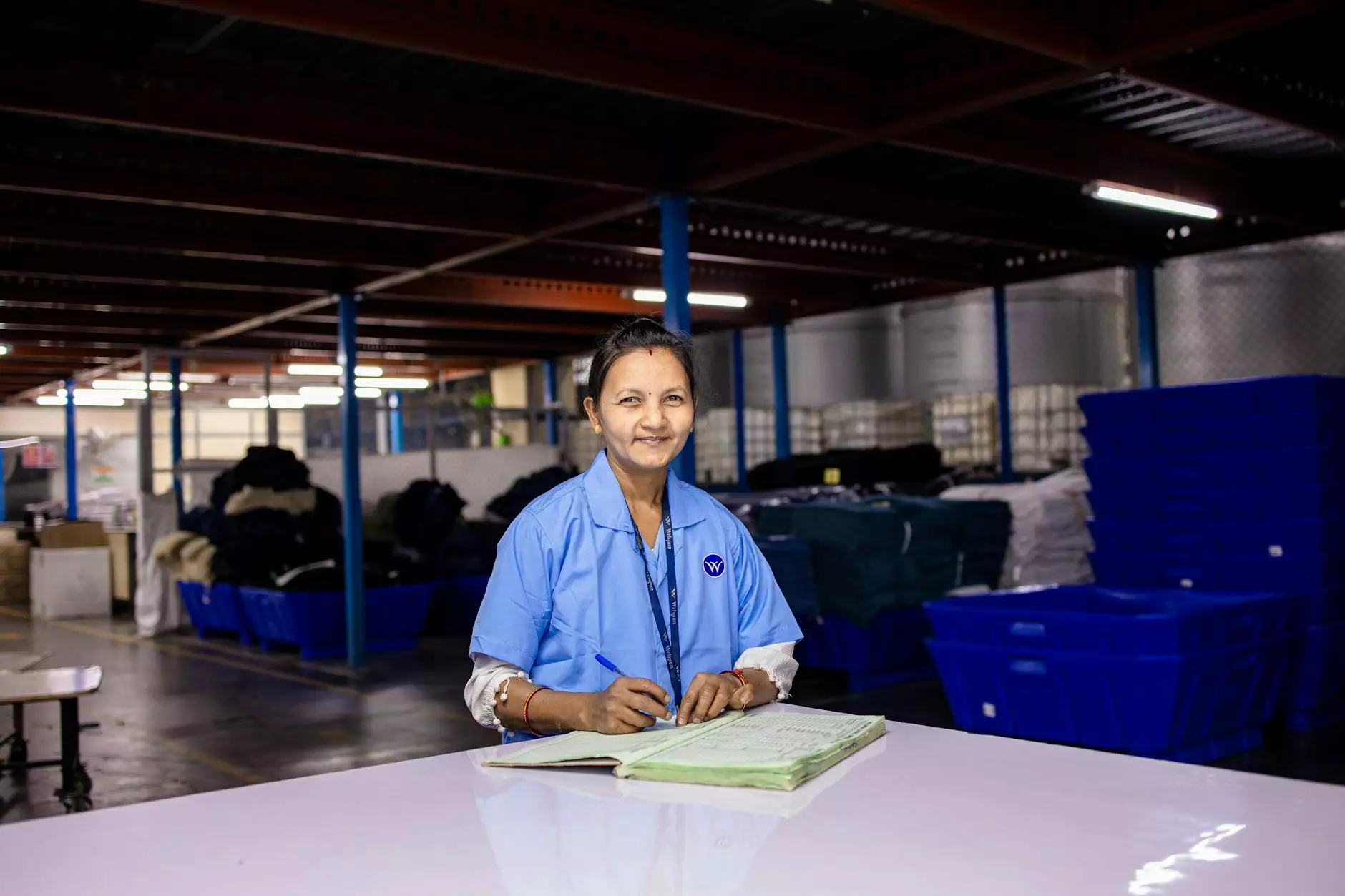
The Foundation of Modern Manufacturing: Plastic Molds
In the competitive world of manufacturing, efficiency, quality, and innovation are paramount. At the heart of many industries lies a crucial component that often goes unnoticed: the plastic mold manufacturer. This specialized field plays an essential role in the production of plastic components, which are integral to various products across different sectors. Whether it’s automotive parts, consumer electronics, or medical devices, the importance of high-quality molds cannot be overstated.
What is a Plastic Mold Manufacturer?
A plastic mold manufacturer is a company that designs, engineers, and produces molds used in the injection molding process. This involves creating mold cavities that precisely shape molten plastic material into the desired form. The process requires a keen understanding of both materials and manufacturing techniques, as well as the ability to leverage advanced technology.
The Injection Molding Process Explained
To appreciate the significance of a *plastic mold manufacturer*, it's essential to understand the injection molding process. Here’s a step-by-step breakdown of how it works:
- Material Selection: The first step involves choosing the right type of plastic, such as polypropylene, polyethylene, or polystyrene. The choice depends on the end product's requirements.
- Designing the Mold: Engineers create a mold design using computer-aided design (CAD) software, ensuring precision and functionality.
- Mold Fabrication: The physical mold is constructed using high-quality metals like aluminum or steel, which provides durability and long-term usage.
- Injection Molding: Molten plastic is injected into the mold under high pressure, allowing it to fill the cavities and take shape.
- Cooling and Ejection: After the plastic cools and solidifies, the mold opens, and the finished product is ejected.
Each step of this process is critical, and a plastic mold manufacturer must ensure optimal conditions and precise engineering to produce high-quality molds.
Benefits of Utilizing a Plastic Mold Manufacturer
Engaging with a reputable plastic mold manufacturer yields multiple advantages for businesses. Here are some key benefits:
- Cost Efficiency: Quality molds produced by professional manufacturers reduce waste and defects, ultimately lowering production costs.
- Enhanced Speed: Efficient mold design and fabrication processes accelerate production timelines, allowing companies to meet market demands promptly.
- Quality Assurance: Expert manufacturers employ rigorous quality control measures to ensure that every mold meets industry standards.
- Innovative Solutions: Collaboration with advanced manufacturers enables companies to access innovative molding solutions and the latest technologies.
- Sustainability: Many modern plastic mold manufacturers focus on creating eco-friendly molds that support sustainable manufacturing practices.
Key Technologies in Plastic Mold Manufacturing
The landscape of plastic mold manufacturing is continuously evolving, driven by advancements in technology. Here are some key technologies currently shaping the industry:
Computer-Aided Design (CAD)
CAD systems allow for precise modeling of mold designs, facilitating intricate detailing that ensures the perfect fit and finish of the final product. This technology also enables manufacturers to simulate the injection molding process, predicting potential issues before production begins.
3D Printing
Rapid prototyping through 3D printing has revolutionized mold creation. Manufacturers can create prototype molds quickly, assess their functionality, and make necessary adjustments without incurring high costs or lead times associated with traditional methods.
CNC Machining
Computer Numerical Control (CNC) machining helps in the precise cutting and shaping of molds. This technology minimizes human error and ensures a high degree of accuracy, leading to consistently high-quality products.
Choosing the Right Plastic Mold Manufacturer
Selecting a plastic mold manufacturer is a critical decision that can impact the success of your production line. Here’s what to consider when choosing the right partner:
- Experience and Expertise: Look for a manufacturer with a proven track record in the industry and the experience to handle your specific needs.
- Quality Certifications: Ensure that the manufacturer adheres to quality standards such as ISO 9001 to guarantee that their processes meet high-quality benchmarks.
- Technological Capabilities: A manufacturer that uses the latest technologies will be better equipped to produce high-quality molds efficiently.
- Customer Reviews: Investigate customer testimonials and case studies to gauge the manufacturer’s reliability and customer service.
- Customization Options: The ability to customize molds to meet specific product requirements can set a manufacturer apart from the competition.
Case Study: DeepMould.net - A Leader in Plastic Mold Manufacturing
One of the leading names in this field is DeepMould.net, a cutting-edge plastic mold manufacturer that excels in delivering high-quality, customized molds for a variety of industries, including automotive, consumer electronics, and healthcare. With extensive experience and a commitment to innovation, DeepMould.net stands out due to its focus on:
- State-of-the-art Facilities: Equipped with the latest technology, DeepMould.net ensures precision and quality in every mold it produces.
- Expert Team: With a team of experienced engineers and designers, they can handle complex projects, offering tailored solutions to meet unique customer needs.
- Commitment to Sustainability: DeepMould.net prioritizes sustainability, using eco-friendly practices and materials in its manufacturing processes.
Their dedication to quality and customer satisfaction has made them a trusted partner for businesses seeking reliable plastic mold manufacturing services.
The Future of Plastic Mold Manufacturing
As the global market evolves, the demand for innovative and efficient manufacturing solutions continues to rise. The future of the plastic mold manufacturer industry is likely to include:
- Increased Automation: Automation can streamline production processes, reduce labor costs, and improve accuracy.
- Greater Customization: As consumer demand grows for personalized products, manufacturers that can provide customized molds will thrive.
- Sustainability Practices: Continued emphasis on eco-friendly solutions will shape the practices of plastic mold manufacturers moving forward.
Conclusion
In summary, the role of a plastic mold manufacturer is vital in the manufacturing ecosystem. By leveraging advanced technologies, prioritizing quality, and implementing sustainable practices, these manufacturers drive innovation and efficiency in countless industries. As companies like DeepMould.net continue to lead the way, the future of plastic mold manufacturing holds promising potential for businesses looking to excel in today’s competitive market.